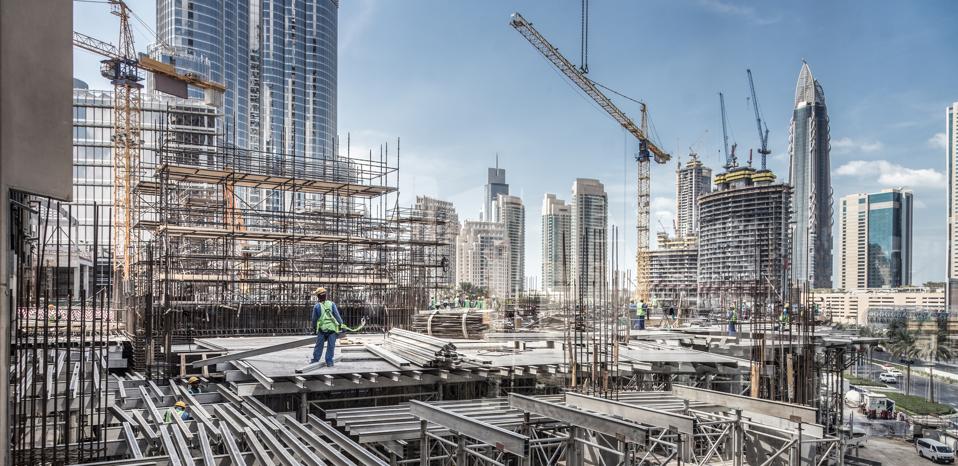
Laborers working on modern constraction site works in Dubai. Fast urban development consept.
getty
Over the past few weeks, thanks to the very successful vaccine rollout in countries such as the US, the UK, and Israel, we have glimpsed the end of the road in terms of the COVID-19 pandemic. We are also starting to see the beginnings of the much-longed-for post-crisis acceleration in demand for construction activity. Alongside this, there has been a massive surge in construction technologies in recent times, driven by strong investment figures into the sector. According to London-based proptech and tech investor Concrete VC, “venture capital investment growth in construction tech has far outpaced the overall VC space.” With this in mind, I had a chat with Autodesk Senior VP and General Manager Jim Lynch, who broke down the main findings of the design and construction software company’s 2021 Construction Outlook report and shared his view on what we can expect for the future.
The report uses U.S. Census data, construction starts data, Dodge Data & Analytics data, and aggregated bidding data from Autodesk Construction Cloud’s BuildingConnected, where over a million owners, general contractors, construction managers, and subcontractors answer or request bids. It is worth noting that this data is very much U.S.-centric and excludes small market players, across a variety of asset classes.
As Lynch puts it, “the big takeaway is that the market is back”. Commercial real estate bidding activity has surpassed pre-pandemic levels, and the BuildingConnected data reflects that real-time bidding has bounced back to pre-pandemic levels and reached an all-time high of 36% year on year in January. Canceled and delayed projects are coming back online, and what is most interesting is that 80% of bids are being turned around in seven days, indicating that the industry is turning to technology to drive greater efficiencies.
By 2050, the global population will have grown by two billion people, and it is a fact that the construction industry will not be able to serve their needs unless it innovates, drastically. The report highlights a series of key concerns that need to be addressed with great urgency so as not to stunt future growth. Of these, the most pressing are around labor market limitations, construction costs, and the design process.
Put simply, the question around the labor market is “how do we fix it”. Lynch shared that it is a global issue for customers, as everybody is concerned about not having sufficient labor to fulfill contracts. According to the report, the hardest positions to fill are laborers, carpenters, and heavy equipment operators as far as crafts are concerned, whilst project managers and construction supervisors are the hardest to find for full-time positions. Lynch reckons that the industry needs to do a much better job at engaging with universities, unions, and labor groups to ensure new entrants into the workforce gain the skills they require. Autodesk makes sure that graduates are proficient in its tech by providing its software for free to universities, partnering with them to ensure that their curriculums include learning to use it.
MORE FOR YOU
Lynch shared that they are also very committed to engendering diversity in construction, stating that, “A year ago we did a project with the Associated General Contractors of America to provide PPE [personal protection equipment] for women in construction. Building out diversity in the workforce is a huge opportunity for the industry and we want to play a part.” These are small steps in the right direction – over 90% of the construction industry is male, and it is imperative that this change, especially in light of ever-growing labor shortages. The good news is that the deployment of tech on-site is bringing opportunities to diversify the workforce, as the industry is becoming less and less manual labor-intensive. According to Lynch, “Robotics is coming to the worksite, and they will not take jobs away, they will make the workforce on the site more efficient and make their jobs safer. What happens on-site is changing, but not fast enough!”
Anybody who is involved with construction will by now be aware of how rising raw material costs (especially those of steel and lumber) are squeezing construction firms’ already slim margins. In many cases, these costs are putting a halt on production, as prices quoted at the end of 2020 are no longer viable. I asked Lynch what the solution might be for this price fluctuation issue in the long run, and he told me that, “The answer is to target greater efficiency during the planning and design cycle. We need to look at different ways to build to cut waste. At Autodesk, we believe a good way to drive efficiency is to look at what other industries are doing – we should manufacture offsite, rather than build on-site. Prefabrication reduces waste significantly and creates more predictability in the process since a factory environment is a controlled environment. Tech isn’t the savior for everything but plays a huge role. For example, Autodesk Takeoff allows for more accurate quantities in preconstruction. After all, a lot of the industry over-purchases, so tech that drives more accurate quantities is important to limit the effects of rising raw materials costs. The next steps revolve around the efficiency of the movement of materials, which we aren’t yet involved in, but work with partners engaged in that aspect.”
You can’t think of efficiency without taking sustainability into account. With real estate and construction producing a third of CO2 emissions, ad a significant chunk of global waste, everybody in the value chain must strive to do better. Barron’s ranked Autodesk fourth in its top 100 most sustainable companies in 2021 and Lynch shared that they are committed to using technology to help their customers become ever more sustainable. For example, Autodesk recently announced a partnership with MultiGreen, a tech-enabled real estate development and operating company, to help power Workforce Plus, its new plan to build 40,000 economically and environmentally sustainable tech-enabled housing units by 2030 across ten states in the U.S.
Last but not least, the report highlights the importance of improving the design process to reverse project margin erosion. According to it, projects with more than 6% of construction value in change orders showed margin erosions. Lynch shared that, after years of making progress to drive efficiency on the design side with its REVIT and BIM products, Autodesk is now working to do the same for construction with its Construction Cloud. He stated that “We have created a common data environment on our single data platform (Autodesk Forge) which all of our tools sit on and push data in and out of. Third parties can also work on that platform. There is a lot of great tech on the market, but the difference in our approach is that, while there are a lot of point solutions out there, we think there is the most value for our customers if we can connect processes and share data. We want to make sure design changes are quickly reflected so we can reduce waste, and we provide a common data environment and change management capabilities. The problem we are working to solve is that of how we collect feedback on issues from the job site and get it back to the design office so these can be quickly addressed.”
There is a lot to unpack in this report, but for me, the key takeaway is this: there is a golden opportunity for the construction industry not just to bounce back from the COVID-driven crisis, but to use this moment to take an innovative leap forward and tackle the structural issues that have historically held it back in terms of growth, productivity, and profit margins. Let’s not waste it.