In 1987, the US government led a collaborative initiative with a dozen semiconductor manufacturers that were on the brink of collapse due to innovative competition from overseas manufacturers.
The federal government led the charge of this consortium, called Sematech, in order to gain and sustain a healthy place in the growing market of semiconductors, pulling off a very successful program that remains strong today.
Now, the building environment faces a similar threat. Developers are ordering modular units from overseas that are price competitive with what could be manufactured in the US and also incorporate more design, construction and operational innovation.
The Need for Collaboration
As Sematech saved the semiconductor industry by investing $100 million per year for five years, Nolan Browne, a serial entrepreneur and founder and chairman of ADL Ventures, wants the federal government to intervene to rescue modular construction, restoring American manufacturing jobs and creating a better built environment.
Browne is relentless with his ideas, contacting government officials to get support to bring prefabrication to the next level, thankful for its appeal to both sustainable- and capital-minded parties. His message is simple but complicated. Today, prefabrication in the United States is stunted. The small manufacturers that exist cannot invest in research and therefore cannot produce the more sophisticated projects that are needed today. Plus, the regulatory environment is so restrictive here in the US, that in many cases, it can be less cost to ship a project over from a more experienced or innovative fabricator.
So, some work is going overseas.
Projects such as citizenM Hotel in New York that was shipped from Poland and a student housing project at UC Berkeley that was shipped from a Chinese fabricator are good examples of the outsourcing.
Not only does the US need to invest in research and development for modular in order to compete on a global scale, it also needs to invest in order to sustain innovation for future cities and to maintain the economy on a broader scale. When these projects go overseas, the fabricators use locally sourced products and local employees. Getting this business back on US soil would boost both the labor market and building product sales.
No Shortage of Limitations
Some US-based fabricators understand their limitations – whether they are design constraints or cost constraints – which are all true business challenges.
Tyler Schmetterer, founder, chief marketing officer and chief sustainability officer at New World Home, a New York-based prefabrication builder, moved his family to Switzerland to learn more from the industry where it is already leagues ahead.
Schmetterer also traveled to sustainable construction conferences in all neighboring countries to learn how each is using prefabrication. What he found is that the penetration of prefab in the US at about 3% is trivial compared to European countries, where it is about 30% in Germany, more than 35% in Austria, and more than 80% in Sweden.
He believes that one of the critical aspects holding the US industry back is the lack of a more turnkey solution.
“In the states, most prefab projects are only about 50% of total costs [of a project] because you have finishing that needs to happen on site,” Schmetterer said. “In Europe they have turnkey offerings. The factory takes care of pulling permits, design work, energy modeling, certification process, delivery, set and final finish on site. The factory also can turn over to the customer and service the house as well.”
Which leads to another challenge that Nic Brathwaite, chief technology officer at Katerra, a construction technology company, has identified.
“The adding of manufacturing creates a layer of complexity inside the organization,” he says. “Engineering and design concepts have intent that has to be interpreted by skilled people in the field. The manufacturing equipment doesn’t have the ability to understand intent. It requires more design completion and much greater collaboration.”
So, Katerra has been working to advance the prefab industry with collaborations to make a more seamless process when creating a digital twin of the end product so the factory equipment has a guide.
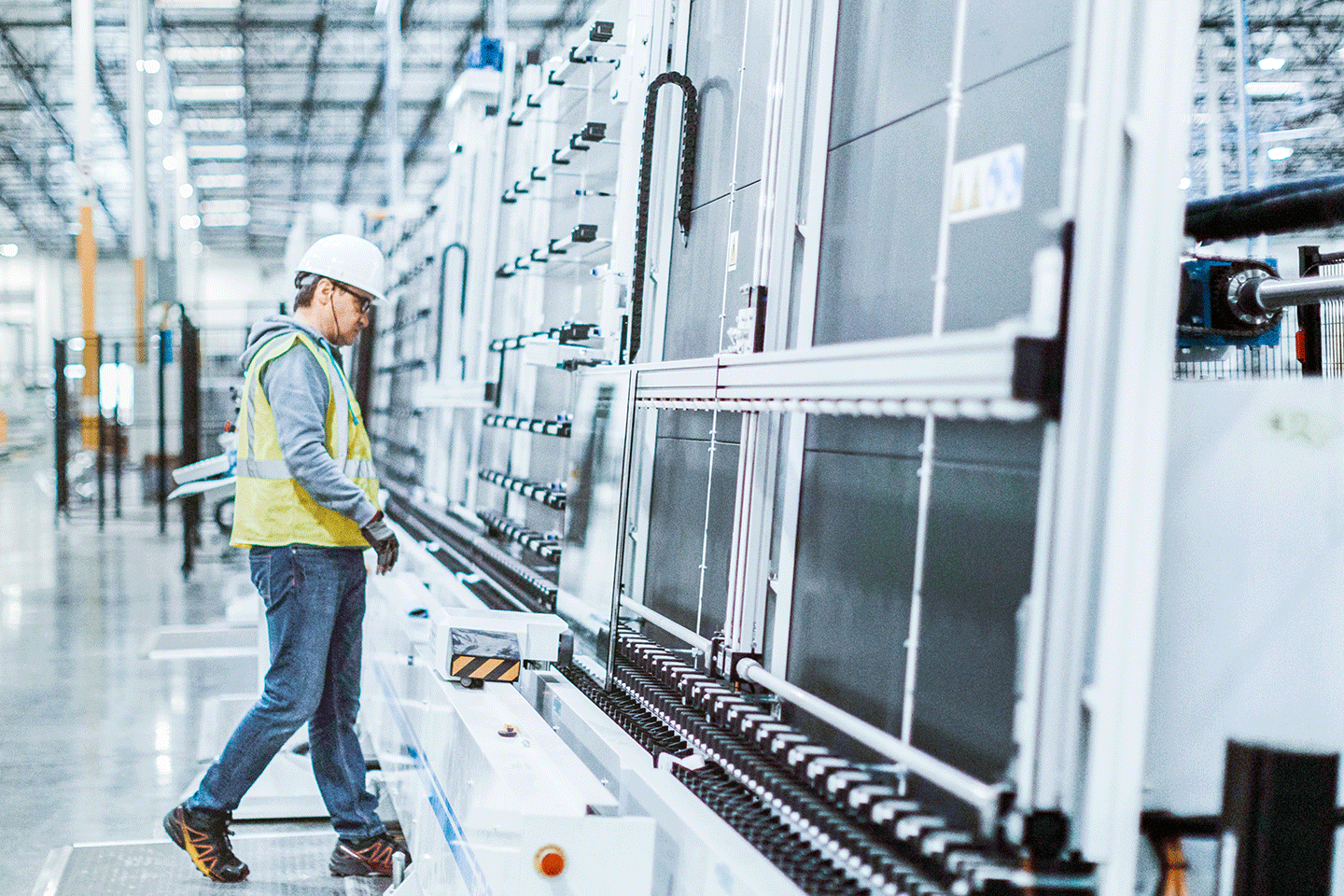
Katerra’s 577,000 SF advanced manufacturing facility has fully automated wood frame wall production … [+]
Katerra
Ken Semler, president at Impresa Modular, a franchising organization with more than 20 factories across the country. is hitting the same obstacle.
“As an industry, we are not as automated as people think,” Semler says. “We do 3D renderings with our customers, fully dimensioned plans, but when we turn it over to the factory, they still have to redraw them. We aren’t there yet, but I see that as being a big opportunity. Not just design systems, but pricing systems as well. The goal would be to design a house in front of a customer and price it as quickly as possible. There is lots of opportunity for integration. We have only scratched the surface.”
Steve Glenn, CEO at PlantPrefab, a California-based custom home designer and builder, looks at the most pressing themes in housing and then partners with great architects to make incredible design accessible to more people as part of its LivingHomes series. The company recently partnered with Koto, a Scandinavian design firm with years of experience in sustainable prefabricated housing to create a LEED Platinum certified home line.
“Our bigger challenge is how can we do it more efficiently,” Glenn says. “We need to integrate a much greater level of automation. We want to be in a position to do custom projects, urban projects, more efficiently because it’s what the market needs. It needs lower cost, higher quality, more sustainable housing. Particularly for cities, you can’t do the same thing over and over.”
Uniquely, PlantPrefab is relying on its factory made for custom work to remain flexible to do modular and panel solutions in order to respond to other challenges as well, like the dimensional and shipping issues that some projects present.
Others are thinking about the cost challenge.
“Our structural system for mid- to high-rise projects is pretty costly, so if we can drive that cost down we can drive the cost of the building down,” said Roger Krulak, CEO, Full Stack Modular, a fully integrated modular builder. “We can do that with crafty engineering or a material science breakthrough. I also see the value of having a truly accurate common single source of information will make it so that you can manufacture buildings by many disperse subassemblies sort of like car manufacturing.”
Brathwaite is seeing the same thing at Katerra, but also sees a solution.
“If you look at construction industry, most innovation happens in the supply chain where a lot of R&D work is being done,” he said. “It’s difficult to get that innovation into the market because of resistance from architects and builders. By better collaboration between companies like Katerra and the supply chain, we can help influence the R&D activity so that it is more likely to be adopted. Because of [our] vertical integration, we can represent a more frictionless channel for getting innovation adopted, to motivate more R&D.”
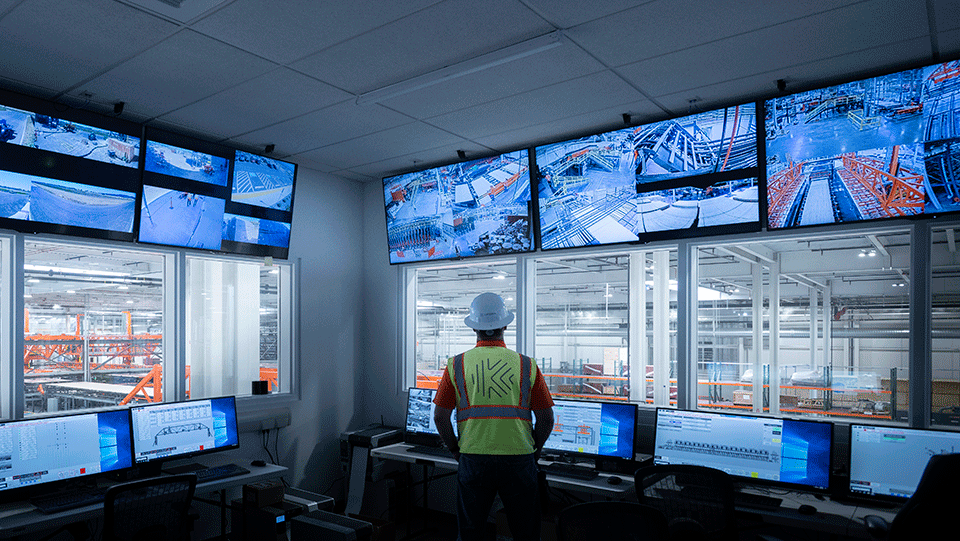
Katerra manufactures cross-laminated timber for its projects at its 270,000 SF facility in Spokane … [+]
Katerra
Finally, of course, there is always the challenge of regulation. Edie Dillman, CEO, B.Public, a startup panel designer that is partnering with manufacturers, and her partner Jonah Stanford, co-founder and chief technology officer, identified the greatest need of the industry as on code acceptance because currently the paths are fairly limited and outdated.
Challenges Aside, The Possibilities are Endless
“The promise of good prefab in America is the promise of the iPhone,” Browne said.
Moving construction offsite into factories holds a lot of promise for efficiency and for innovation.
A well-designed building would incorporate an energy management system that can connect to the grid, occupancy sensors, and air quality sensors, all from the beginning built into the building.
“A hospital could be a perfectly controlled environment and would know how the operating rooms are being used,” said Browne. “Resource efficiency goes way up.”
Having the design complete up front and the construction happening at a faster pace also means that soft costs, such as design work, real estate fees, inspection fees, project management, and taxes, are minimized. Since soft costs typically make up about 30% of the total construction cost, this has the potential to make a big difference, especially as providers start identifying new ways to adapt their products and services to prefabrication and modular.
For instance, fabricators could start managing more of the way that things are financed and insured to not only minimize the number of policies on a project, but to have an insurance wrapper that covers the entire process.
Browne suggested that this level of innovation will require standards that can be graded and qualified, from the fabricators to the architects.
With his time in the much more mature market in Europe, Schmetterer also sees incredible opportunity for more sustainable construction, so he is taking an active hand in creating a consortium with fabricators worldwide as a knowledge sharing platform on sustainable practices and also trying to create guidelines with Passive House to deliver to the factories in a proactive approach to more net zero construction.
A requirement for all new construction in Europe to be nearly net zero by the end of the year is quickening the pace there, and in Austria, fabricators are building to Passive House standards, the most rigorous building performance system in the world. This progress was helped by government funding and incentive programs in those countries to build more sustainably.
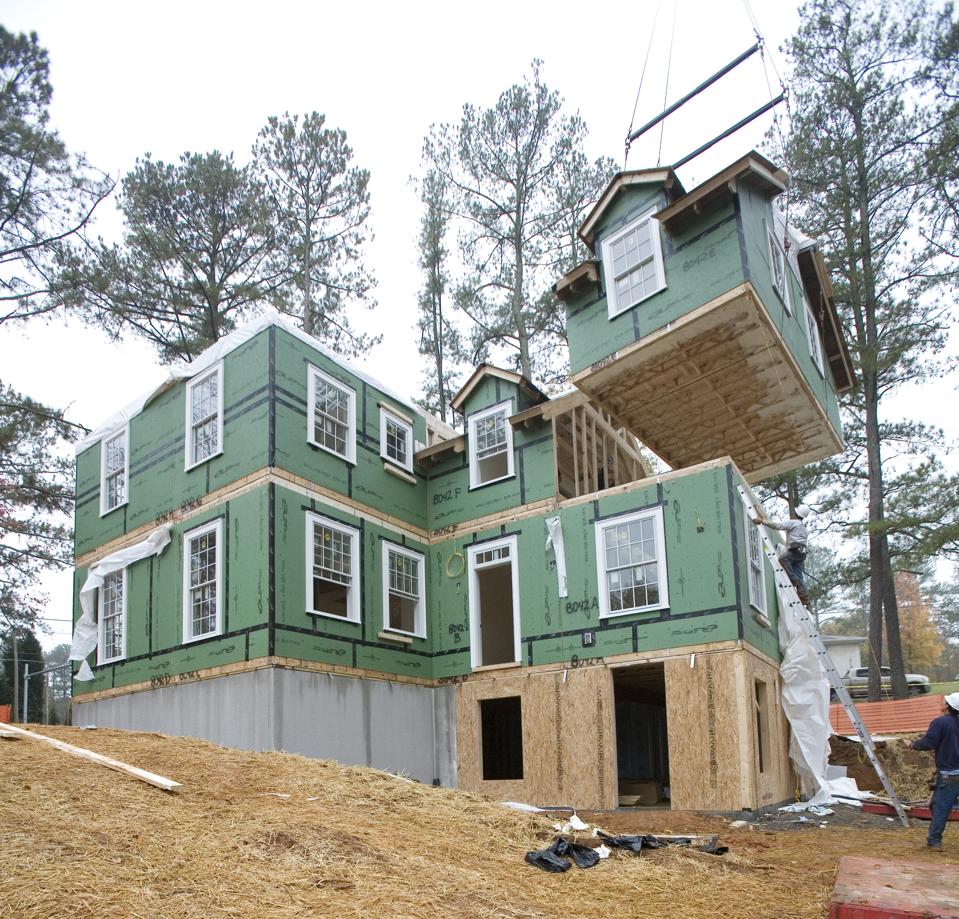
During a one-day set, the final module of eight is being placed on this New World Home LEED Platinum … [+]
New World Home
These standards have the ability to massively improve building performance. Manufacturers that are using Passive House requirements have been able to create homes ‘out of the factory’ that can reduce energy consumption by up to 90% versus conventional built homes, reported in this recent study of 2,000 Passive House certified buildings.
Collaborating for COVID-19 and Cost Improvements
While Browne appeals to the federal government for an official program, others are taking this into their own hands. Vaughan Buckley, founder and president of Volumetric Modular Companies recently launched the Modular Mobilization Coalition to create emergency medical housing for COVID-19 patients that could later be repurposed for permanent use as supportive or apartment housing.
After gaining traction with the emergency housing project, Buckley saw the benefit of collaborating to build buying power, join in revenue sharing projects, share resources and leverage investments.
Buckley expects to grow the Modular Mobilization Coalition to represent the majority of US volumetric modular manufacturers and is already at 28 members that represent nearly 25% of the US industry production of International Residential Code and International Building Code construction. Buckley anticipates that with the force of the group, just the volume buying alone would result in between 20 to 30% savings on technical components and other finish goods.
The promise of those savings is inspiring and so is the rest of the collaboration, because operating alone as a startup or small business can present a lot of challenges.
Buckley is skeptical of the term fully automated manufacturing, sharing that no such operation exists. Very little of a modular factory’s daily operations can actually be automated, between all the various functions—design, regulation, IT, finance, HR, sales, resales, marketing, warranty, QA, storage, logistics, supply chain, finishing, assembly, fabrication, engineering—few are truly able to be automated by the fabricator. Most current factories are limited to augmenting design or engineering and automating only fabrication and framing. This would equate to automation of about six percent of daily operations, according to Buckley.
Tim Sullivan, senior managing principal at real estate consulting firm Meyers Research, is excited about the potential of this group and its efforts because of the enhanced level of quality that comes with modular construction.
His firm is studying the opportunity for more modular and prefabrication by identifying the markets that have the most potential for a conversion from conventional construction. Sullivan’s research considers the design of the home, the site’s distance from factories, along with any other factors that bring challenges to the traditional model that could be removed with the new process.
Inspiring the Future
Buckley is not stopping there. His incessant drive for more innovation has him peering into the future to create a virtual version of his manufacturing facility. Artificial intelligence sensors use video and microphones to track what type of work is being performed by the audio signature it puts out—such as a nail gun or a saw—identify issues, allowing for the organization to be more predictive.
He has dreams of going completely virtual but right now the capital resources stand in the way. Spending millions to virtually test a single line modification may not make sense, but to do so for the benefit of dozens of factories will, and in the future this technology will reduce cost. Going completely virtual would allow him to run a complete project through a virtual factory, to know how many people will be needed and to know how much time a project would take to complete.
It also would help change the parameters of how building products are made. Buckley could visualize and get true results from using a 60-foot sheet of plywood instead of an 8-foot sheet that is specifically made for human installation on the job site. When those parameters are lifted, many more trials can take place to tease out more efficiencies.
“Material manufacturers are the key to new products for the industry and most are hesitant to make new products without knowing their ability to penetrate market share,” said Buckley. “MMC helps make this more feasible for manufacturers to innovate and test new markets on a large scale in partnership with a large coalition.”
I encourage all those interested to get in touch with Buckley and Browne to support their passion for progress in the industry. Its promise is something we need to focus on for more affordability for tomorrow’s housing.