Housing had an extraordinary year in 2020, resulting in about 1,380,300 housing starts according to a report from the U.S. Census Bureau and the Department of Housing and Urban Development. That is up seven percent from the year before, and it is due to an even larger increase in the completions of single family detached housing.
While the demand for all types of housing is strong, there is still a massive gap in what would be considered supply that is affordable. For instance, Arthur Nelson, professor of urban planning and real estate development at the School of Landscape Architecture and Planning at the University of Arizona, reports that less than three percent of the housing completions in 2019 hit the missing middle, or were at price points that would be considered affordable for those earning between 80% and 120% of the area median income.
The lack of growth in wages also plays a critical role in housing affordability. Property data company, ATTOM Data Solutions, reports that in the fourth quarter of 2020, the nationwide average wage fell below what would be needed to purchase the typical home. According to a September 2020 US Census Bureau report, the median household income in the US in 2019 was $68,703. That median income breaks down to $55,000 in take home pay and $2,115 in pay checks every other week, which depending on your math, would afford a home around the $150,000 range.
Yet, the median sales price of homes in December 2020 was $355,900 according to the US Census Bureau, which is out of range for anyone at or below median household income.
Business data platform Statistia published a list of the median household incomes in the top 25 most populated cities in the US in 2019, and 16 of them are lower than the national average, with Detroit’s at just $33,965. In Detroit, this would afford a home around the $80,000 mark with a low down payment.
Plus, experts predict that prices in 2021 will just keep rising. Building material costs are higher nearly across the board and builders in a monthly survey conducted by housing market research firm Zonda, report that higher costs are the biggest concern for 2021. Zonda’s chief economist Ali Wolf also noted that land costs are up six percent year-over-year because of declining inventory.
MORE FOR YOU
Housing expert Ivy Zelman expects to see a six percent increase in home prices this year, as she stated in a recent conference organized by real estate company Inman.
What’s needed now is innovation.
Innovation Lab Creates More Attainable Housing Solution
Clayton Homes is the nation’s largest manufactured and modular home builder, and recently launched The Home Innovation Lab to rethink the home building process and to therefore make housing more affordable.
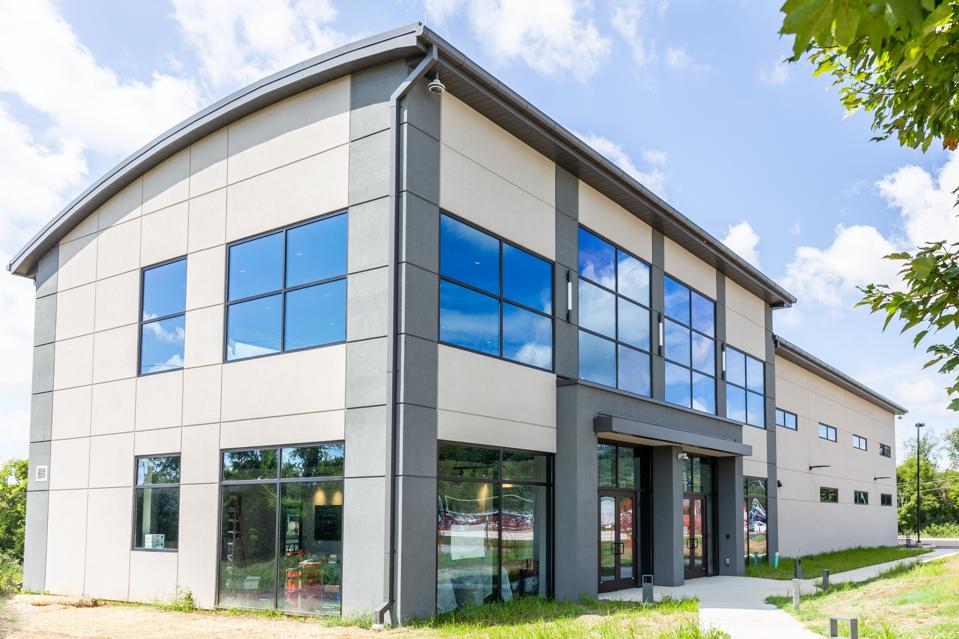
The Home Innovation Lab opened in October 2019 to offer more collaboration across the Clayton … [+]
Clayton
“Really the overall approach of the Innovation Lab is to create collaboration with engineering, design, and construction teams,” said Megan Foster, interior design manager with Clayton Home Building Group. “The new process helps maintain affordability and increase efficiencies and marry it all with appropriate design along with what a buyer expects to see.”
Opened just before the pandemic shutdowns in October 2019, the company’s Innovation Lab is a 5,000-square-foot space that is open to tap into teams that work at each of Clayton’s 40 facilities because each group is unique in how it builds homes. The space is meant to bring diverse teams together, including the company’s architects, engineers, 3D renderers and interior designers, to collaborate and create process efficiencies.
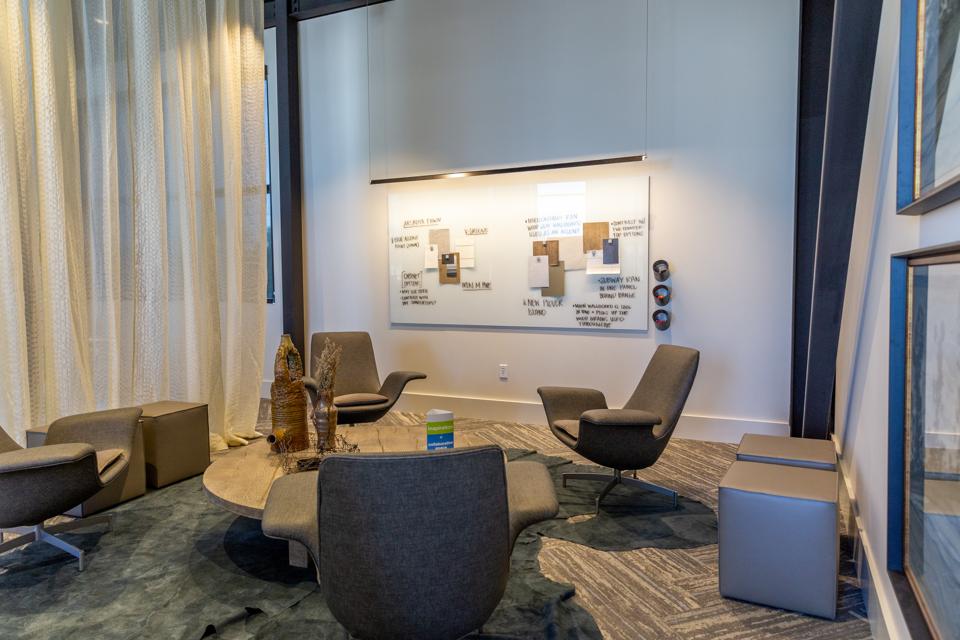
Space in the home innovation lab is available for all functions.
Clayton
The cooperative approach is supported with technology, such as virtual reality tours of a new home plan during the design process to share new concepts and to talk about how it is going to be built before it gets built.
“It’s crucial to think about how we are innovative in the materials that we use and also how we are increasing efficiencies to provide houses faster,” Foster said. “We have learned a lot. We have found that the more detailed, the better. When the site teams can visualize it, they start to talk about the way they are trimming windows, which might be different than what they see in the virtual space. They also might see an issue with cabinet doors that open the wrong way or that are a different size. With the virtual process, we can immediately change something or bring in a new material to be more efficient.”
Not only does the technology improve the efficiency of the process, it also lowers the waste of materials and dials in a concept before it’s built. The team also is able to factor in the reduction of waste in the process as well.
The objectives of the lab have been realized with Clayton Homes most recently launched brand.
“Because of the process, we were able to lower the cost of the homes,” Foster said. “There was a line of homes, Epic Homes, that went through this process. It gave us the opportunity to use the lab. Epic launched first thing in 2020. We took all the new technology features and really honed in and polished the design process that integrated the tech and the production-friendly mindset to make sure it’s a really good-looking house at the end of the day.”
The Epic Collection is a series of twelve homes that meets the needs of the masses and delivers to the country’s much needed short supply of workforce housing. Starting prices in the Epic Collection range from $60,000 to $120,000 not including delivery and installation, with floorplans that span from 1,020 to 2,280 square feet.
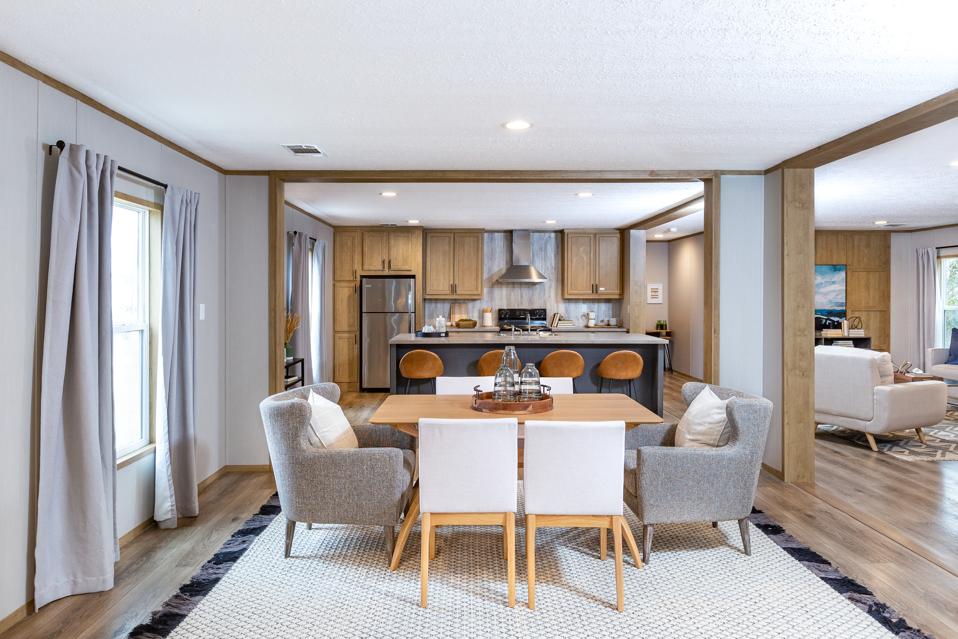
The Epic Collection of homes came from the new Home Innovation Lab process and offers price points … [+]
Clayton
This home series, like all Clayton homes was manufactured offsite, or built in a controlled environment not subject to outside elements, where energy usage can be monitored and waste minimized. Plus, the process is faster, which also leads to lower costs.
“We were given a price range to stay within, but we were also challenged to go further and extend our capabilities with material management team,” Foster shared. “We had to maximize materials and still hold ourselves responsible to deliver something that consumer wants. People are now living at home more than ever, so Epic really focused on how people live within their homes and the space planning aspect.”
The integrated and collaborative team reaches out to customers to understand them better and incorporate those learnings into the process.
“We just conducted a survey that justified that we were on the right track,” Foster said. “It was perfect timing with the launch of Epic. It allowed us to clarify what consumers want and pushed us even further with innovation.”
On A Smaller, More Holistic Scale
Tim Swanson lives and breathes passion for his mission. Swanson spent nearly three years as the chief design officer at Chicago-based construction company Skender, trying to launch a manufacturing facility that would allow the company to deliver housing more efficiently to more deserving households.
The pandemic put the facility’s opening plans into a tailspin and Swanson had to reimagine his career, launching right into founding a new company, Inherent L3C. This new home building company uses modular construction as the foundation to deliver more affordable housing.
The company’s first project is four single family homes on infill property owned by the City of Chicago. Swanson plans to manufacture the homes in a temporary space in May for four deserving families to move in this August.
“Modular affords the opportunity to provide a safe and consistent work environment for employees, removes weather from the equation for continuous production and through both supply chain and standardized systems, and drives both material cost and production time down,” Swanson said. “This affords Inherent L3C the ability to produce a home at a fraction of the time, six weeks versus six months, with a certainty that for the most expensive purchase a family ever makes, a level of quality and finish that matches this reality. Further, by leveraging socially-aligned partners, removing construction financing costs from the equation provides additional cost savings for the family.”
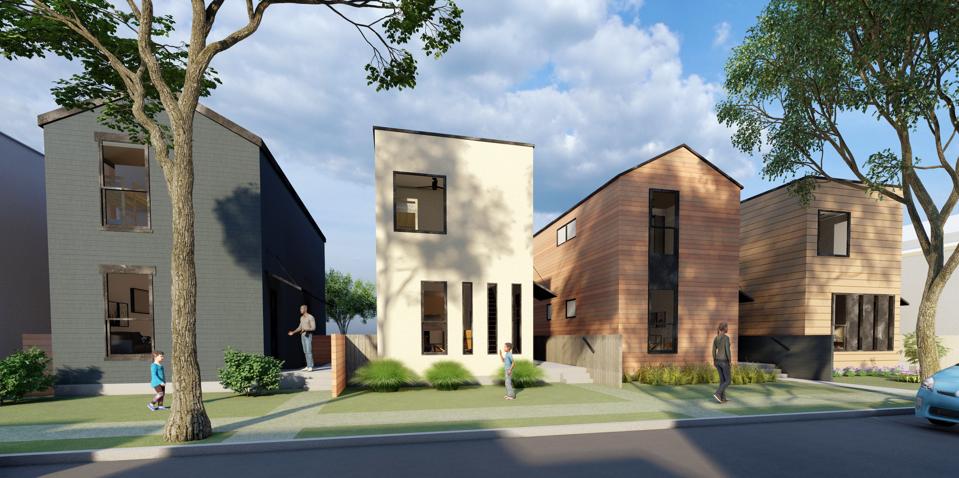
Inherent L3C’s first project will be four modular homes at just $225,000 within Chicago city limits. … [+]
Inherent L3C
Swanson realizes that it’s a long game as he plans with the city to convert vacant property to become a part of the tax base to develop healthier communities. He also is making sense of the finances. He wants to offer homes to families that are both three times their annual income, but also only one-third of annual expenditures.
He points out that in Chicago, the average household of four earns $91,000 and not only cannot afford to purchase a market rate home, but do not qualify for subsidized housing. During the past two decades, there were only six homes sold or built in Chicago for less than $500,000.
Also because of the company’s focus on long-term opportunities for wealth generation and investment protection, Inherent will provide wraparound services to home buyers. Inherent is still detailing the services, but currently has it outlined as a five-year support program that includes quarterly maintenance, life insurance, disability insurance, home insurance, a security system, and even equity in the company.
Framing For The Future
“The sky is the limit at the Innovation Lab,” said Foster. “We are encouraged to explore and try new things. We are constantly challenging ourselves to think outside the box and ask more questions, all while keeping a production-friendly approach in mind.”
Clayton is looking at all aspects of efficiency and collaboration to continue its mission of democratizing housing, making a new home available to a broader spectrum of buyers who otherwise wouldn’t have the opportunity to be home owners.
Perhaps the best part is that Clayton has the scale to produce volume, completing nearly 4,000 new homes each year. While Inherent L3C also is ramping up to create manufacturing facilities across Chicago that will each produce 100 housing units per year.