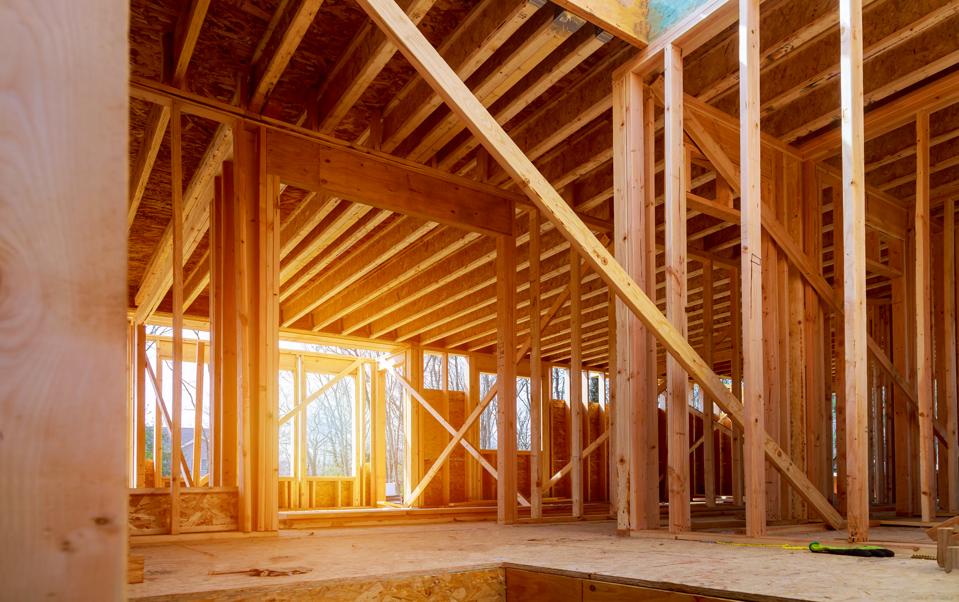
Homebuilders adopt technology to sell homes but face headwinds in construction.
Getty
As the country seems to cautiously lock down in order to stem the spread of the coronavirus, homebuilders are embracing what is now becoming the new normal for the wider real estate industry – going virtual.
Miami-based Lennar Corp, one of the U.S. largest publicly traded homebuilders, is inviting buyers to its online showings and offering drive-through closings, said CEO Stuart Miller on a Thursday conference call.
“Even in the current environment, we are selling homes,” Miller said as reported by The Real Deal. “Since the first quarter, new orders continue to be strong.”
The adoption of virtual solutions to some of the constraints the coronavirus has stamped on home construction underlines a larger, sustained trend in the industry.
“We need to recognize that builders have been selling homes remotely for over 20 years,” says Tim Costello, CEO and founder of Builders Digital Experience (BDX). “This is nothing new. The pivot today is that the tools that builders have at their disposal are substantially different than they were 20 years ago. It makes the process so transparent and frictionless for the consumer, that we’re actually seeing a transition in the market irrespective of the coronavirus.”
From FaceTime showings of model homes to virtual-reality tours that allow shoppers to change features such as countertops and wall colors, technology serves a buffer to the current drop in foot traffic to homebuilders’ sales rooms.
That has been the case for Arizona-based Fulton Homes. “I thought last week we might take a little bit of a dive,” says David Webb, Fulton Homes vice president. “It didn’t happen. Our foot traffic was off a little bit in our sales offices, but our sales were strong as ever.”
And yet, the coronavirus pandemic has roused some impediments for home construction, an industry that has taken years to mend from the 2008 housing crisis and still struggles to meet the demand for new abodes in the country.
Builders’ confidence
The start of 2020 proved a favorable period for homebuilding, registering a post-recession peak in activity. Prior to the coronavirus outbreak, adjusted for seasonality, single-family permits and starts posted strong tallies. In January, year-over-year, permits for single-family abodes rose some 21%, the National Association of Home Builders (NAHB) reported. Last month, seasonally adjusted single-family starts grew by 6.1% to a little over one million.
However, homebuilders’ confidence is slightly wearing off, dropping two points to 72 in March in the latest NAHB/Wells Fargo Housing Market Index. While the homebuilders’ sentiment remains solid overall, half of builders’ responses used for the index were collected before March 4.
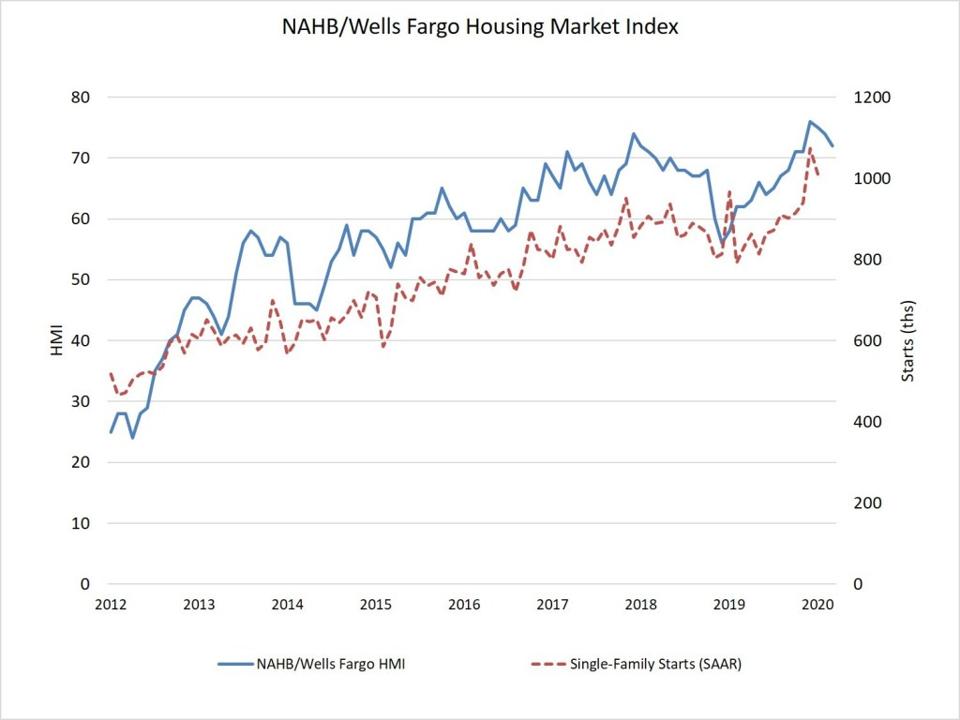
NAHB/Wells Fargo Housing Market Index tracks homebuilders’ confidence, juxtaposed to single-family … [+]
National Association of Home Builders
Supply chain disruptions
The NAHB/Wells Fargo survey indicates that 21% of builders experienced some disruption in supply caused by the coronavirus internationally. The number grows to 33% for builders who replied to the survey after March 6.
“We estimate that probably about a third of residential building material products come from China,” says NAHB Chief Economist Robert Dietz. “There’s certainly a supply chain linkage there.”
Homebuilding imports from China, where the coronavirus first spread before expanding globally, include tiles, various finishes, faucets and sinks, among other products.
Yet, builders face different levels of interruption in their supply chains. Ali Wolf, chief economist at Meyers Research, a real estate data provider and consultancy, says, “some of our clients are saying, ‘Supply chain disruptions are real and we’re struggling to get the products that we need.’ Some of our clients are saying, ‘The supply chain is real, but we’ve found domestic partners, and we’re able to work with them.’ And some of our clients are saying, ‘It’s okay, we’re still able to match what we want with what we can bring into the country.’”
Webb says that Fulton Homes has found alternate suppliers, some abroad and some in the U.S., for the materials it used to purchase from China.
“We had bigger disruptions with tariffs last year,” Webb says.
In this economic downturn, tariffs continue to weigh on home construction, even if firms in different sectors have urged the administration to provide customs relief.
“If, say, tariffs are eased – it has been announced that they won’t be – that can be a positive impact for some builders,” says Todd Teta, chief product and technology officer of ATTOM Data, a real estate data company.
Government regulations
Even if homebuilders can still access needed materials, in some locales they might not be allowed to build. As cities and entire state institute “shelter in place” orders, the construction industry may come to a temporary halt.
The city of Boston placed a moratorium on construction on March 16. Two days later, so did the state of New York. Meanwhile, homebuilding evaded the mandated closures of non-essential businesses in California and Miami-Dade, Florida, for instance.
At the same time, as government employees shift to working from home, securing permits, inspections and certificates may take longer.
A pause of construction activity might prompt furloughs and terminations of construction workers, although Wolf says it is still too early to speculate.
“I don’t think we’re at the point of mass layoffs,” she says. “But I do think that there’s going to be an interesting dynamic, [given that] the homebuilding industry has struggled for workers for a really long time.”
Stock market shocks
Most homebuilders in the country are privately owned, rather small enterprises. As such, they might find themselves insulated from the stock market gyrations that impact the few large publicly traded home construction companies.
At the start of the coronavirus outbreak in the U.S., public builders – much like a slew of other businesses – saw their values drop as the stock market plummeted.
SPDR S&P Homebuilders, an exchange traded fund that tracks the home construction, dipped from a high of nearly $50 in mid-February to $25.60 at the end of the day yesterday.
Despite the stock encumbrances, Costello of BDX says, “the large [public builders] have access to all kinds of resources and talent within their company; to lower cost of capital, lower cost of materials.
“But then, they have the challenge of moving a big ship, because they are a large Fortune 1000 company. If you’re a small regional, privately held [builder], you may not have access to all of those things, but you also can easily call everybody into a conference room, make a decision and change your business.”
Moreover, some private homebuilders might be able to tap into policy stimuli such as business loans and tax deferrals rolled out to cushion the financial blows of the coronavirus.
Still, with a variety of headwinds, which are likely to result in a soft second quarter for the nation’s economy, NAHB’s Dietz says, “there’s a whole series of things that have to happen in order to build a home and I think we’re going to have a real test of that over the next four to eight weeks.”