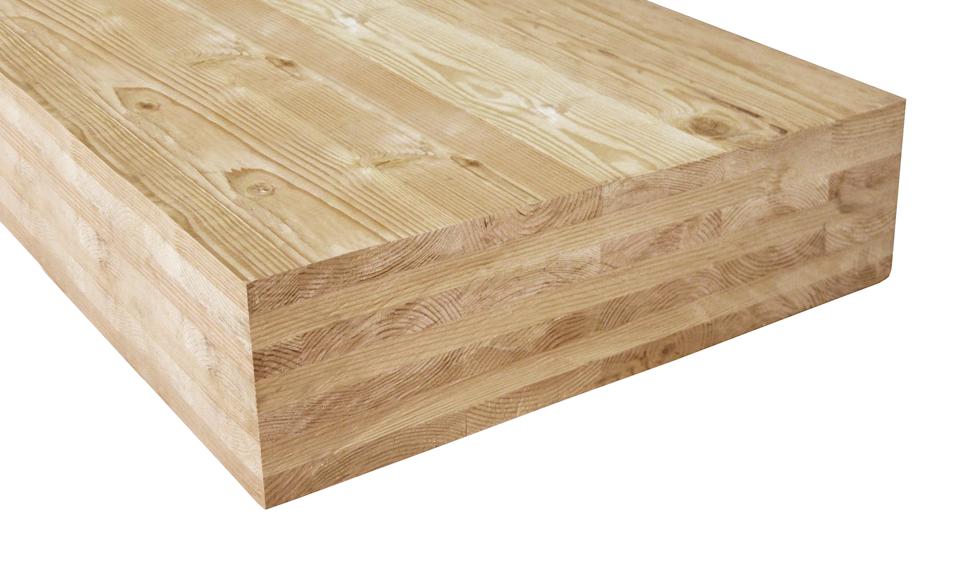
A cross section of engineered wood.
PHOTO COURTESY OF THE APA – TH ENGINEERED WOOD ASSOCIATION
Cross-Laminated Timber (CLT) is comprised of layers of solid wood laminated together at right angles to each other, under pressure, in the same way that plywood is made. They can be 3, 5, 7 or more pieces thick, but always an odd number. Panels can be fabricated as large as 8 ft. by 64 ft. and up to 1 ft. thick. This process creates prefabricated panels that are structurally and dimensionally stable.
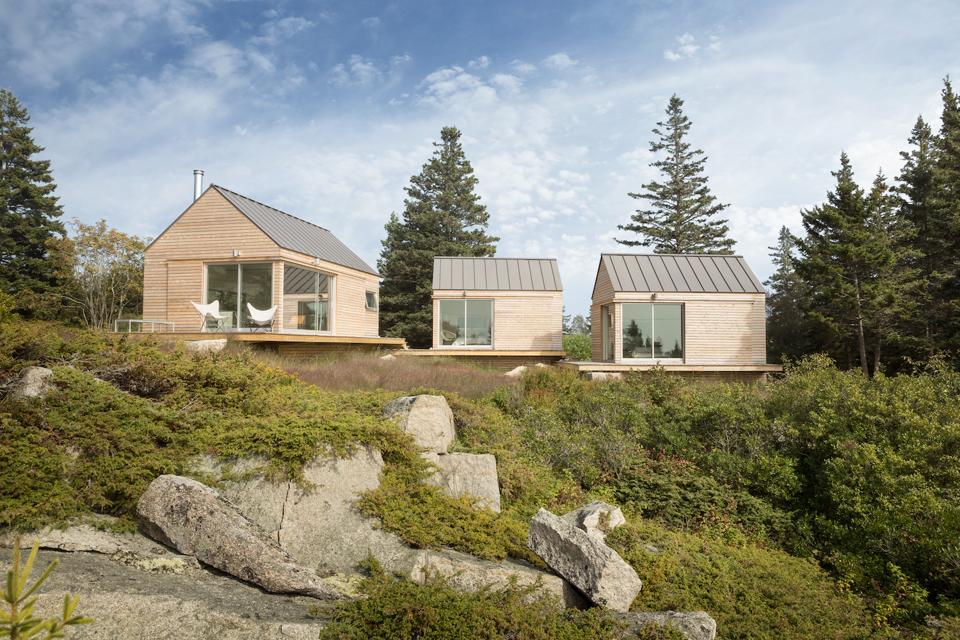
These Little Houses on a Ferry in Vinalhaven, ME were designed by GoLogic, engineered by Bensonwood … [+]
Photo courtesy 0f Trent Bell Photography
CLT panels form the entire enclosure for some houses including —floors, walls, and roofs— and function as both structure and finish to create a minimalist and rustic appearance. However according to Bill Parsons, WoodWorks’ Vice President of Operations, CLT panels are particularly cost effective for multi-story and large building applications. Mass timber products in general are gaining in popularity for office and commercial buildings, schools, public and recreational facilities, etc. where developers and design teams are interested in using sustainable materials and creating beautiful environments that offer biophilic benefits. He says “WoodWorks is also starting to see more multi-family applications. The specific value proposition varies—e.g., a developer may want a unique space that’s leased quickly, hopefully at a premium; a company may want a workplace that fosters creativity/teamwork and reflects a culture of sustainability to attract top talent; and a school board may define their overarching goal as an enriching environment that promotes learning. Mass timber products such as CLT can be used to create customizable spaces with open floor plans and exposed wood structure, so they’re a good fit for these objectives.”
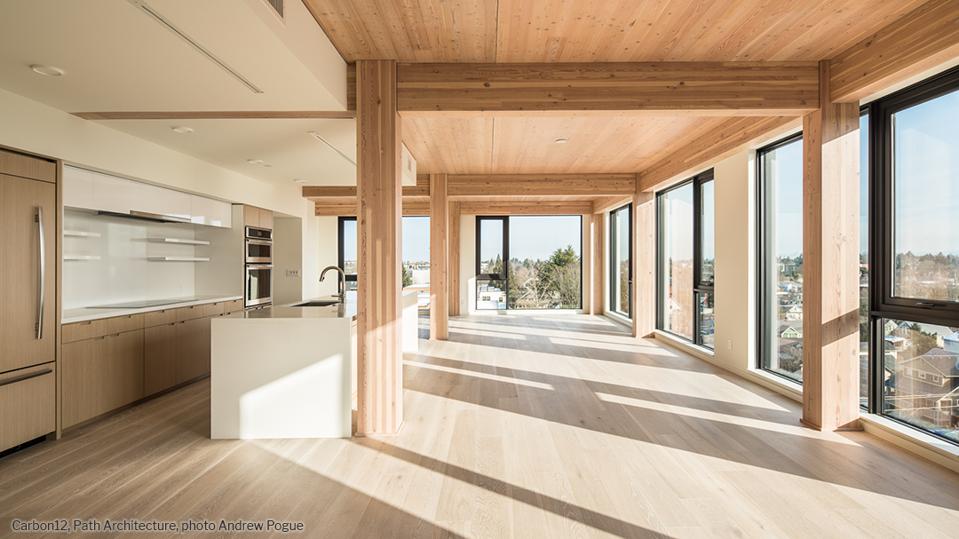
Carbon12 8-story luxury apartment building in Portland, OR. Kaiser+Path, estate developers, … [+]
Photo courtesy of Andrew Pogue
CLT panels offer positive environmental benefits, including carbon storage and low greenhouse emissions during manufacturing, and they are recyclable. The panels reduce construction time compared to some other building methods, require a shorter learning curve for installers, create a healthy environment. It is a renewable material that can be made from relatively small-diameter trees and those affected by insects and diseases, which would not be used otherwise.
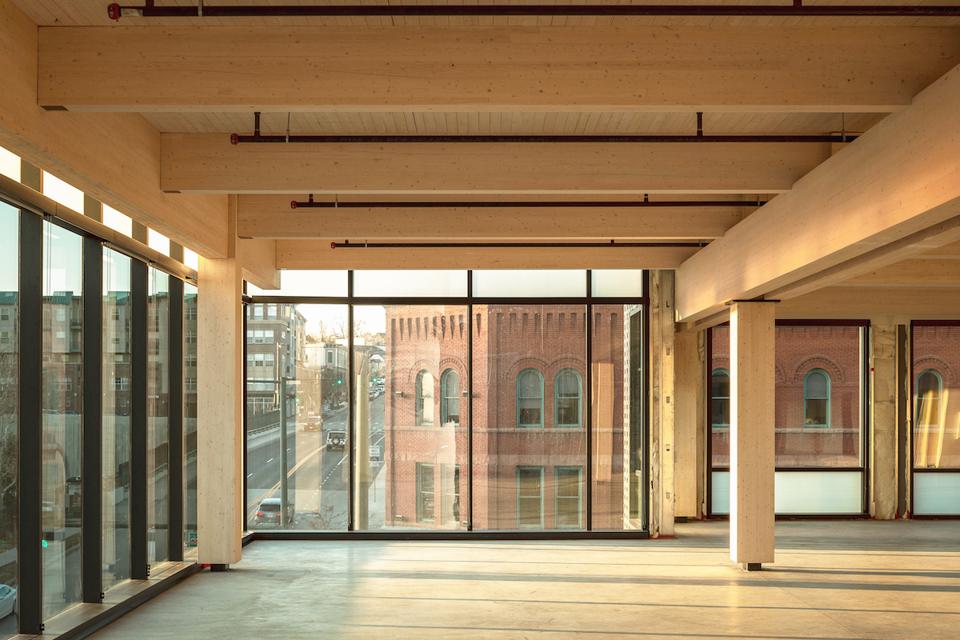
Platte Fifteen office building by Oz Architecture in Denver, CO
Photo courtesy of JC Buck
The panels are precut using computer-controlled milling machinery, a technology called computer numerical control (CNC) machines. Shop drawings are provided with the size, shape, and orientation of each panel. The sequence of packing, unloading, and erecting the panels is carefully choreographed on site. The CLT components reduce on-site labor and can efficiently be assembled on diverse sites—an excellent solution for building structures in remote or dense urban locations where a storage area is limited.

The exterior of the Platte Fifteen by Oz Architecture in Denver, Colorado.
Photo courtesy of JC Buck
In some cases the wood can be exposed on the exterior because of the inherent fire resistance large mass timber panels, columns and beams. According to Parsons, “In a fire, large members tend to retain their load-carrying ability longer than members with small cross-sections; this is because a char layer forms on the surface while the interior remains undamaged and structurally sound. The predictability of wood’s char rate has been well-established for decades and is recognized in building codes and standards.”
For additional information about CLT regarding project support, education, resources for design and construction professionals, check out the website of WoodWorks.