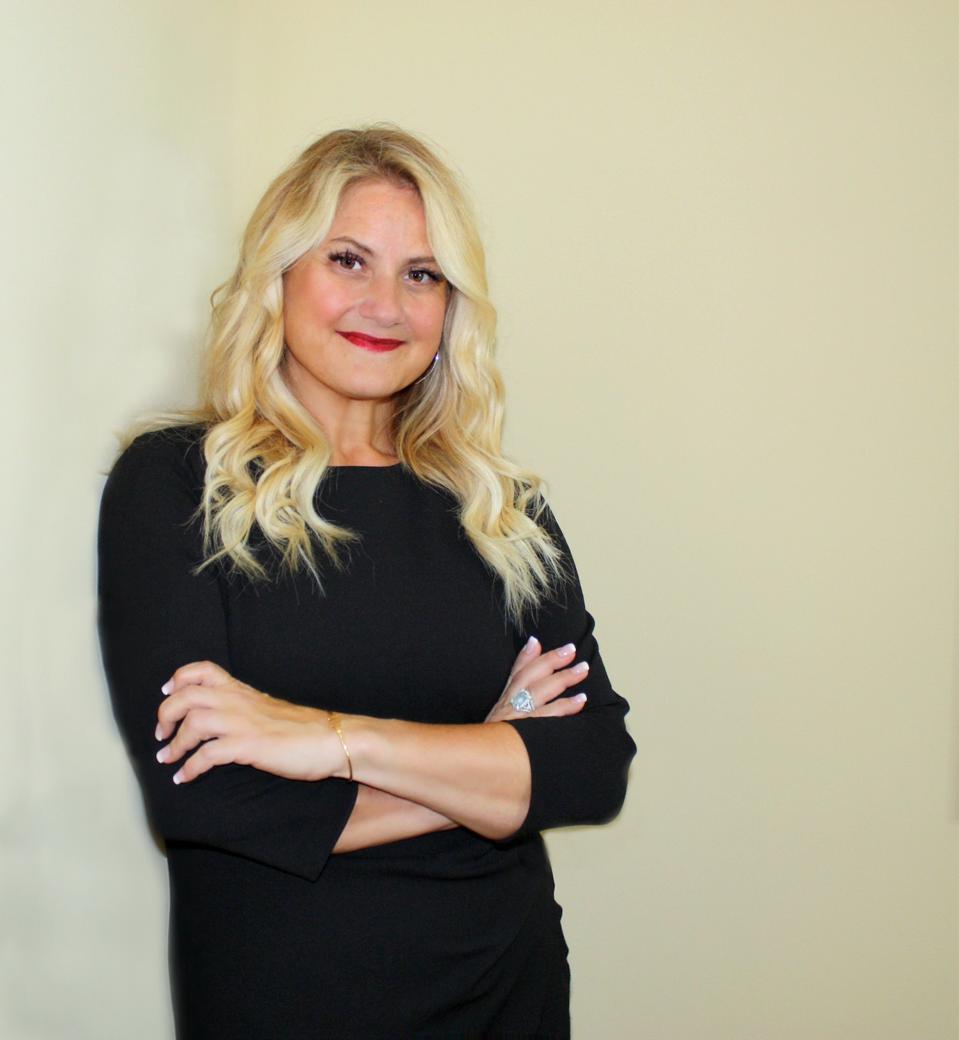
Amy Marks
Photo courtesy of Amy Marks
Known as the Queen of Prefab, Amy Marks is the head of industrialized construction strategy and evangelism at Autodesk, as part of Autodesk Construction Solutions. Prior to joining Autodesk, Marks was the CEO of XSite Modular, where she defined the language and process that is now adopted by companies, countries and builders around the world to enable prefabrication. She has a strong industry following and is frequently chairs and keynotes influential industry conferences.
How is the architecture, engineering and construction (AEC) industry responding to the lack of hospital beds needed for the COVID-19 crisis?
There are a lot of companies stepping up. Many conventional AEC firms like Balfour Beatty, HGA Architects and The Boldt Company, Rosendin and others are responding with prefabricated solutions.
One prefabrication company that is far along in the process of manufacturing for medical facilities is the modular firm BLOX. They are developing mobile isolation care units (MICUs). MICUs typically take months to produce, but BLOX has been able to trim their timeline down to weeks and speed up production using BIM and cloud collaboration technologies like Autodesk Construction Cloud.
Some companies that usually focus on prefabricated housing or classroom units are also pivoting to focus on healthcare. I think it’s safe to say that the AEC industry at large, including prefabrication, is currently helping address our healthcare needs.
What are the advantages of having these hospitals built with prefabrication?
The biggest advantage prefabrication offers is speed. Facilities can stand up much quicker when they’re composed of ready-made components that can fit together, versus when each component has to be developed from scratch.
For the immediate, short-term need, there are already purpose-built ready-made solutions in the form of tent structures, containerized structures and modular temporary structures. If some of these structures aren’t purpose-built for healthcare, they can be retrofitted quickly, which is what has been happening with hotels – except these structures can then also be rapidly deployed to other locations once their first deployment is completed. That eliminates all the waste of retrofitting a hotel and converting it back to its original purpose.
After the immediate, rapid-deployment need has been fulfilled, established prefabrication factories can pivot their operations to provide additional healthcare infrastructure for the long term. Doing so will drive more certainty around costs and reduced schedules for large-scale healthcare projects, compared to those projects that are traditionally built.
Why were they able to build two hospitals in China in 10 days and it takes so much longer in this country?
Back in 2003 when SARS (Severe Acute Respiratory Syndrome) was spreading, China built the Xiaotangshan hospital in Beijing using prefabrication, so the industry there had a great model to reference when building hospitals for COVID-19. Additionally, because the industry in China had experience constructing modular hospitals, there was likely an existing inventory of prefabricated components it could use for building this time around.
This time, we saw China take ready made frames, stack them and fit them out on-site with some prefabricated elements. The US is also doing this in healthcare response. We’re also doing more complicated prefabrication integration for large-scale hospital builds and full volumetric modular, smaller healthcare facilities.
There is now an ecosystem of pieces and parts that is established and growing across the AEC industry.
What are the challenges of accelerating hospital construction under the current approach – i.e. largely without prefabrication? What are the benefits of adopting prefab?
Currently, what’s challenging about healthcare construction is that most project teams approach every build like it’s never been done before. The process doesn’t always draw from previous work, allowing the next build to “stand on the shoulders” of the last project. This results in a slow learning cycle or sadly, loss of institutional knowledge from one project to the next. Everything may be different each time as hospital projects usually procure different architects, GCs, engineers and subcontractors every time.
In short, our industry can be project-centric to its detriment. When you’re working with new partners on each project, you have to figure out how to work with new people and come up to speed on organizational processes every time. That makes it very difficult to bring takeaways forward and make your succeeding builds increasingly efficient, even if you have some prefabrication processes already in place. Prefabrication works best when owners understand the value of the approach and hire teams to integrate it at project conceptualization. Aside from upfront AEC contracts, other downstream procurement methodologies can also limit the ability to use prefabrication on an impactful scale.
Cost certainty is a big benefit to prefabrication. Additionally, different elements – electrical, HVAC, etc. – can be decoupled and concurrently constructed off-site, helping reduce the on-site schedule. The value of this benefit varies depending on the drivers of a given project.
Safety is another major benefit. Manufacturing happens in a controlled factory environment, and the risks typically associated with building on-site are subsequently reduced as well. Having less people on the job site creates a safer job site. The amount of people on a job site will become an important consideration as the construction industry starts back up and needs to take social distancing into account. Job sites also become easier to manage, allowing the team to pay attention to areas that need more management. Ultimately, project teams should look to prefabricate areas that can be cellular in nature and where there is a high level of complexity even for one space. Prefabrication is about increasing productivity.
We’re in the infancy of a growing ecosystem around prefabrication with architects understanding Design for Manufacturing and Assembly (DfMA) principles and incorporating prefabricated standard elements, subcontractors embracing manufacturing themselves and GCs acting as integrators. We’re seeing more owners and the entire AEC community invest in and embrace prefabrication. All are key to the new manufacturing ecosystem for construction. Couple this with collaboration tools and the digitization of project information, and we’re on a very promising trajectory.
Can you tell us more about how hospital construction can benefit from prefabrication, even outside of the COVID-19 use case?
For healthcare facilities in particular, prefabrication can also minimize interferences to the patient experience by reducing disruptions to operating campuses and their surrounding areas. This can create a healthier environment that is safer to all and improves the patient experience. There are benefits that impact the bottom line for everyone involved in hospital projects, and the healthcare construction industry is taking note – it is actually ahead of other sectors in adopting prefabrication for this reason.
Accelerating healthcare construction’s adoption of prefabrication may be a silver lining to COVID-19, and hopefully adoption will ripple throughout the entire construction industry to deliver the infrastructure we need to support our growing populations around the world.