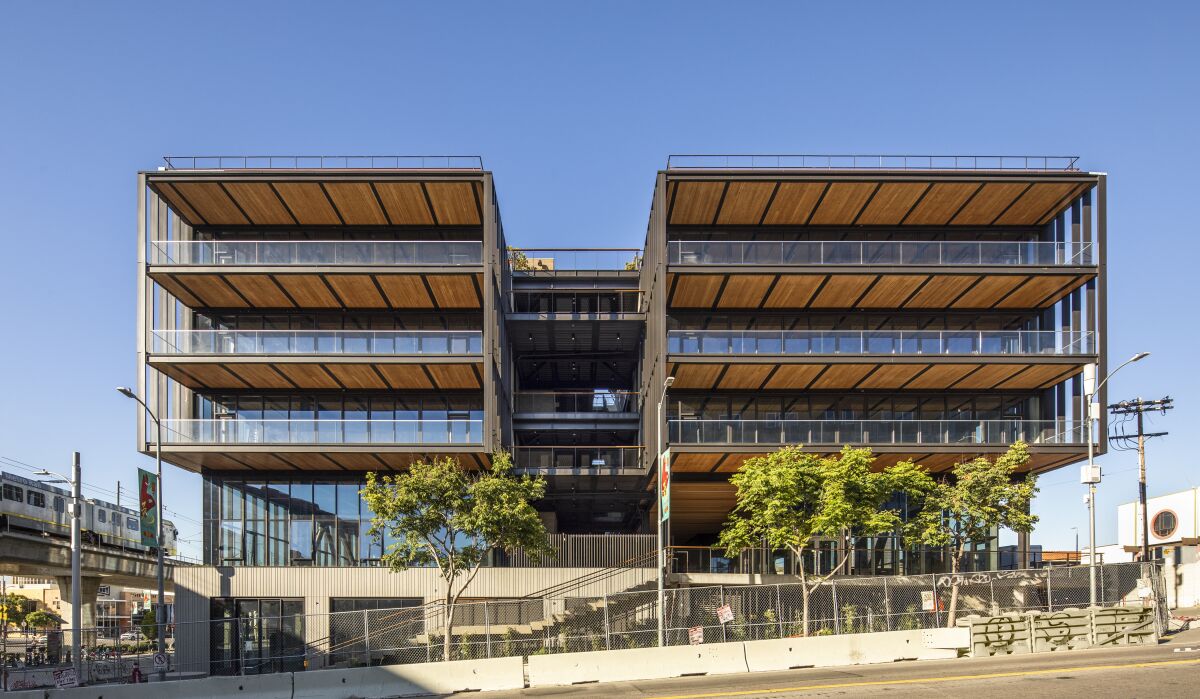
The mixed-use structure at 843 N. Spring St. designed by Lever Architecture is one of the largest mass timber structures in Los Angeles.
(Paul Turang)
From a distance, the building under construction at 843 N. Spring St. in Chinatown might seem like many of the commercial structures popping up around L.A.: four stories of open-plan offices rise above ground-level retail spaces that one day will house restaurants and shops. But move in closer and you’ll find some surprising details‚ including a ground-level arcade dotted with rough tree ferns and a rooftop patio planted with foxtail agaves and purpletop vervain. What is most notable, however, is wood — which is everywhere.
Look up and you’ll find that the building’s floor plates are partly supported by broad panels of mass timber, the generic term used to describe a variety of industrial, engineered woods. 843 N. Spring is part of a wave of such structures springing up around the United States. In Milwaukee, you can find a new 25-story mass timber residential tower, and a forestry college in Oregon now inhabits a pair of graceful mass timber buildings.
It may seem counterintuitive, but mass timber can match or exceed the strength of concrete and steel. Also counterintuitive: The material performs well in a fire. (In much the same way a large log will fail to ignite in a campfire, mass timber’s solidity is not conducive to rapid fire.) And, in fact, it has been subjected to a battery of testing both in the U.S. and abroad, including blast tests that have allowed for its use by the military.
Thomas Robinson, co-founder of Lever Architecture, a firm with offices in Portland, Ore., and L.A. that has helped pioneer the use of mass timber in the U.S., says, “It’s very different from what you buy at Home Depot.”

An atrium features landscape design by James Corner Field Operations.
(Myung J. Chun / Los Angeles Times)
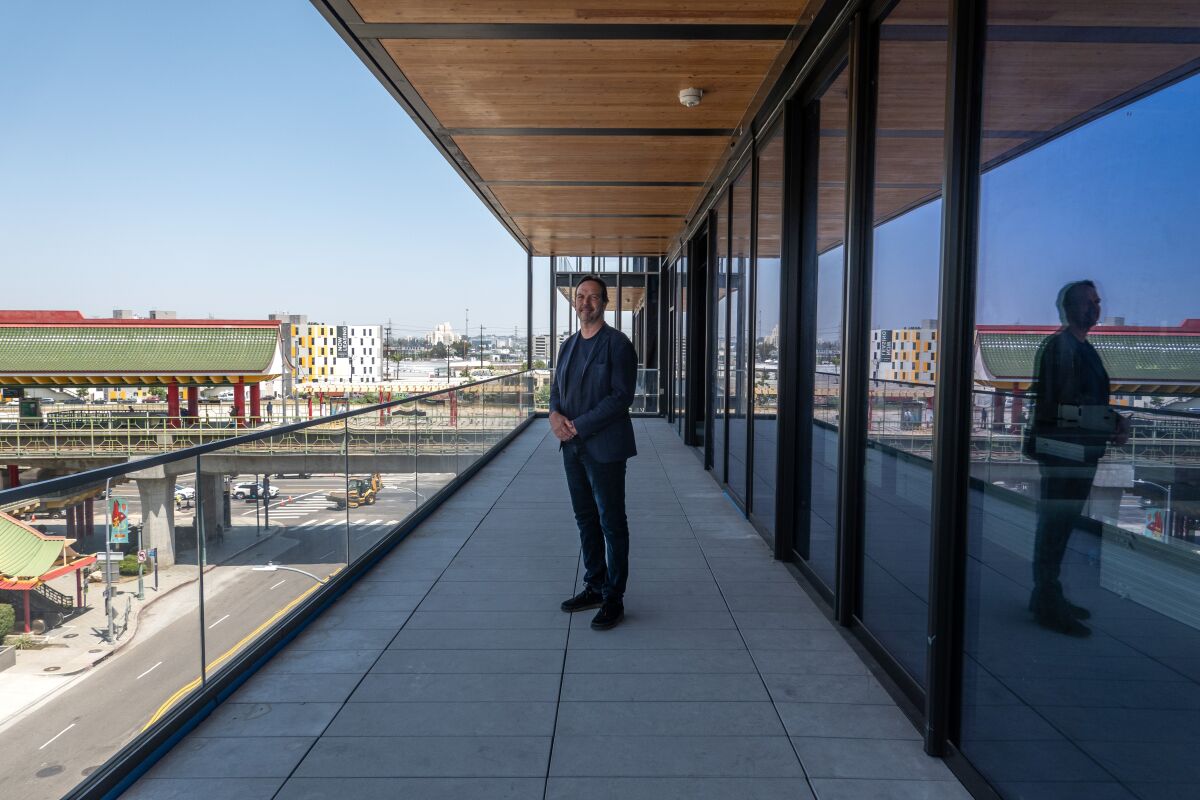
Thomas Robinson is a co-founder of Lever Architecture, which is known for its mass timber projects.
(Myung J. Chun / Los Angeles Times)
Among Lever’s projects are mass timber buildings for Adidas and the Oregon Conservation Center in Portland. The team is also behind the thoughtful design at 843 N. Spring, which includes landscape design by James Corner Field Operations (the studio behind the remarkable Tongva Park in Santa Monica).
At the moment, 843 N. Spring is probably the largest structure employing mass timber in Los Angeles, though it could soon be outdone by a mixed-use development at the border of Culver City and West Adams designed by Shop Architects. Whatever its scale, the building is an intriguing example of the possibilities of the material.
Trees, for one, sequester carbon, and unlike concrete and steel they don’t require intensive fabrication processes — they just grow. A study published in 2019 in the Journal of Building Engineering, which examined the use of mass timber from harvest to construction, found an average reduction of 26.5% in global warming potential. Mass timber is also produced in prefab panels, which means it can be milled to the specific dimensions of a project, thereby limiting waste, staging and construction times. If a mass timber building is torn down, wood can be reused. Concrete is not nearly as flexible: When it meets the wrecking ball, it generally ends up as landfill.

Mass timber was used in the floorplates of a hybrid structure in L.A.’s Chinatown for L.A. developer Redcar.
(Myung J. Chun/Los Angeles Times)
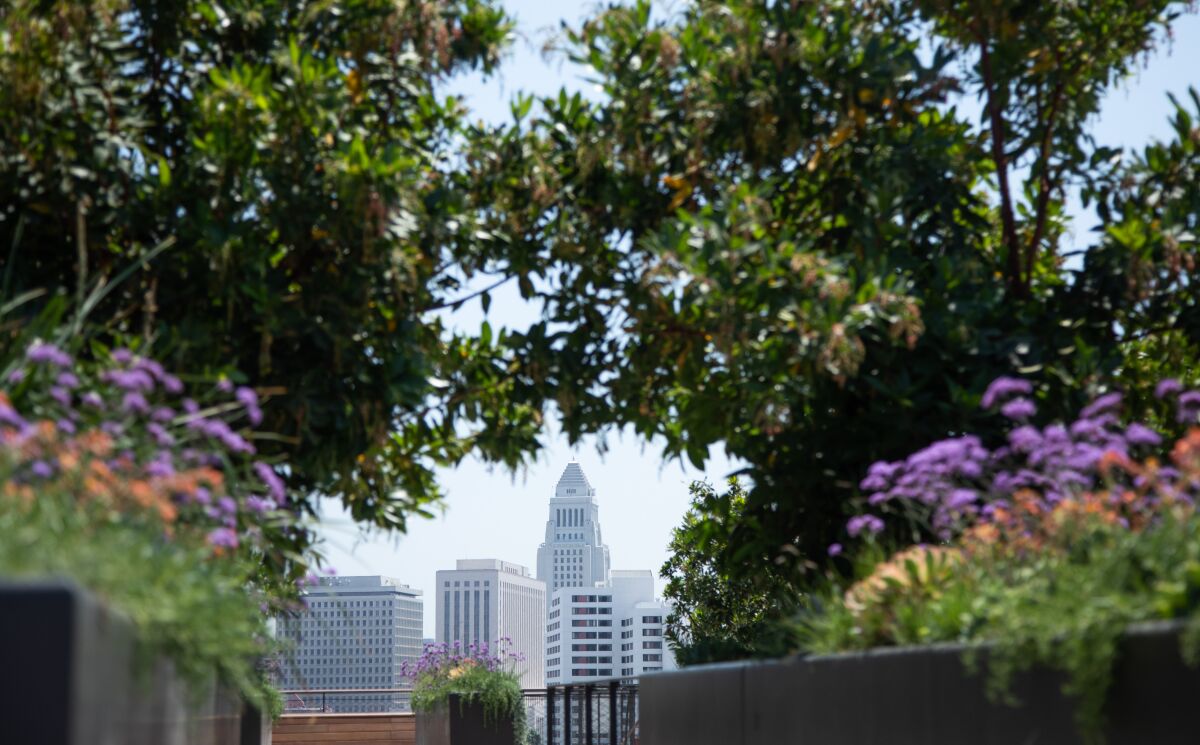
A view of City Hall from the rooftop at 843 N. Spring St., which features landscape design by James Corner Field Operations.
(Myung J. Chun / Los Angeles Times)
Certainly, just because it’s wood doesn’t make it environmental. Clear-cutting, for example, is devastating to local ecologies. “Part of our job is to ask the right questions,” Robinson says. “You’re really trying to identify forests that are managed in a way that really thinks about sustainable forest practices for the long term.”
Lever prefers wood that has received sustainability certifications from the Forest Stewardship Council, which includes the timber used in the Spring Street project. Transport to the site is also key. Wood for the building was harvested in British Columbia and transferred to L.A. by ship, which is less carbon intensive than trucking it in overland.
The Spring Street building is a hybrid structure, meaning it still employs steel and concrete. But this is mitigated by other elements in the design.
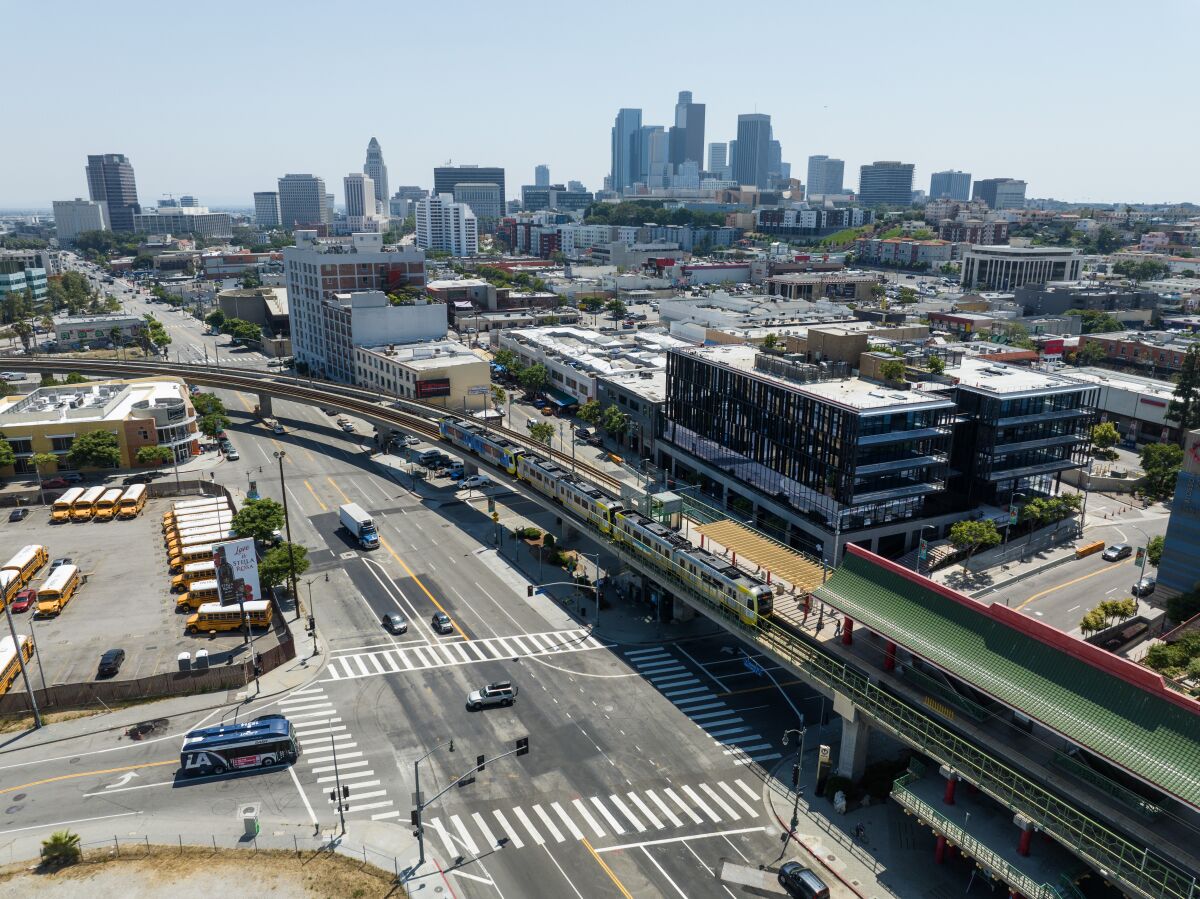
843 N. Spring St., in the foreground at right, is next to the Chinatown Metro station.
(Myung J. Chun / Los Angeles Times)
Rather than tear out the vacant big-box store that inhabited the site, the architects built on top of it, thereby avoiding additional emissions and demolition waste. In the existing underground lot, they added stacked parking, which made room for additional cars without more digging, and — more important — added generous bicycle storage. (The building practically sits on top of the Chinatown stop of the A Line, making it an ideal hub for multimodal transit.) Unusual for a commercial building, the design also prioritizes fresh air: Each unit has operable windows and sliding doors that allow for passive ventilation.
No building can be carbon-zero — construction consumes resources. But the process can be far less carbon intensive. And, as 843 N. Spring also proves, it can look really good.